Why don’t EVs have four in-wheel motors?
In-wheel of wheel-hub electric motors are not a new idea. The Lohner-Porsche petrol-electric hybrid of 1900, for example, was powered by electric motors built into the hubs of its big, balloon-tyred wheels.
Today, in-wheel electric motors are to be found in plenty of EVs. It’s just that none of them are mass-production cars or SUVs. Bosch-made in-wheel motors are popular in small electric motor scooters, like those produced by the Chinese brand Niu. Direct-drive hub motors are also fairly widely used in electric bicycles.
READ MORE: Full electric car advice and FAQ
READ MORE: EV tech explained
Still, some companies are developing four-wheeled EVs with in-wheel motors.
Want the latest EV news and reviews delivered to your inbox? Subscribe to our weekly newsletter!
US-based Lordstown appears to be the manufacturer closest to production. Founded in 2018, the start-up’s plant in Lordstown, Ohio, was bought from General Motors. GM also invested a reported US$75 million in the company.
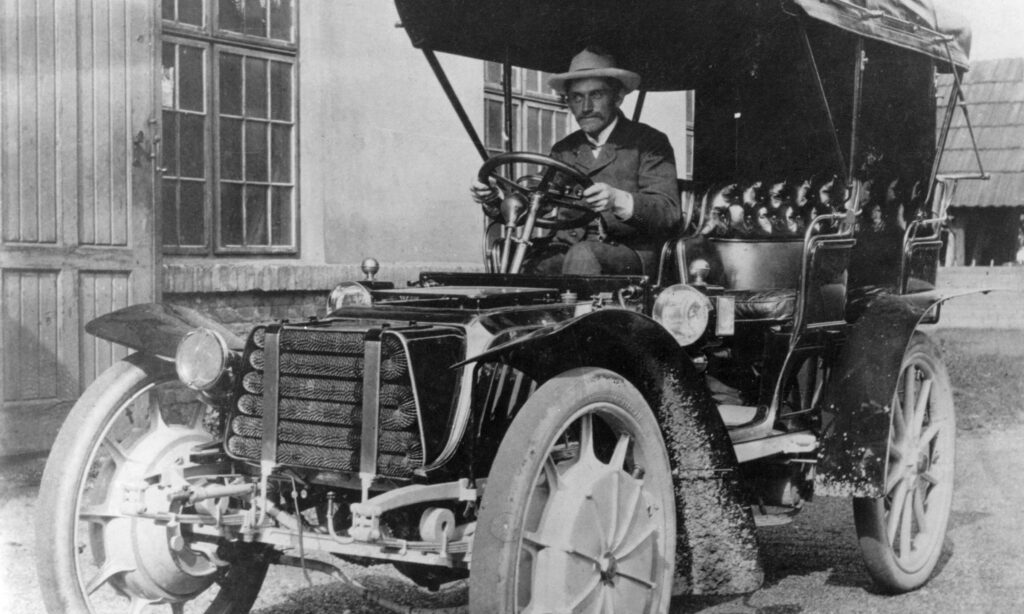
The Lordstown factory is building pre-production versions of its first model, the Endurance ute. Full-scale production should begin in September 2021, and the company says it’s holding 100,000 (non-binding) pre-orders for the big double-cab pick-up truck.
Although Lordstown is making the motors inside each of the Endurance’s wheels, credit for the their design belongs to a company called Elaphe. This Slovenian outfit has a licensing agreement with Lordstown.
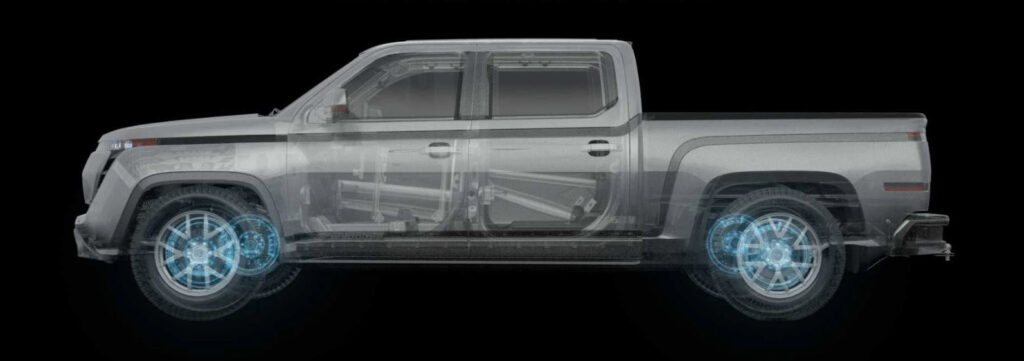
The Endurance has “The World’s First All-Electric In-Wheel Drive System Built For Work,” according to the capital-letter enthusiasts in the Lordstown marketing department.
The Lightyear One isn’t anything like the Lordstown Endurance, but it also features four in-wheel motors. Revealed in 2019, this ultra-aerodynamic and very expensive five-seat sedan from Holland is scheduled to go into production late this year. Lightyear’s efficiency-obsessed engineers designed the motor used in the One’s wheels from scratch.
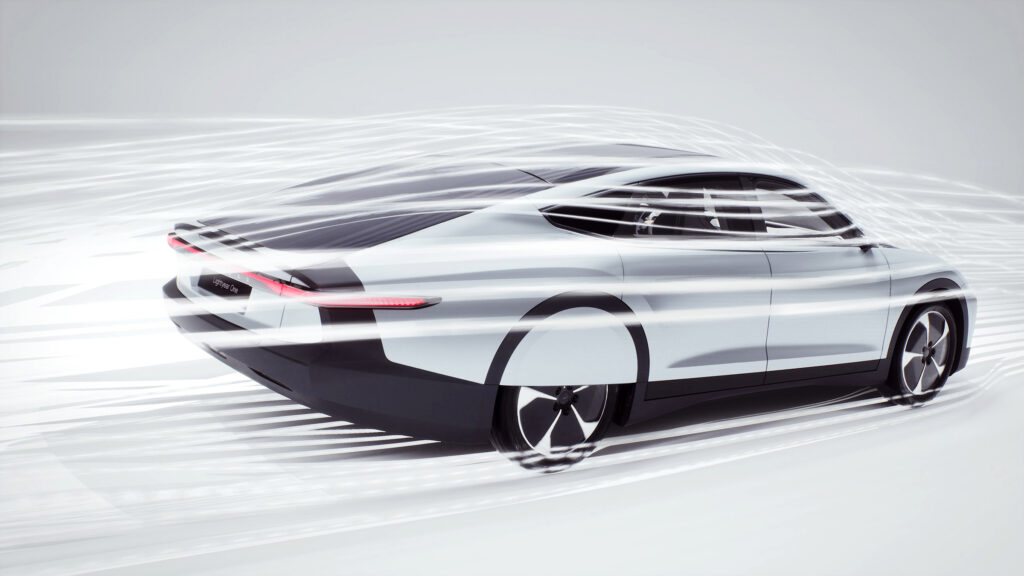
Both Lightyear and Lordstown stress the benefits of in-wheel motors. They’re simple, energy-efficient and save space, they say. What they don’t mention is that there are disadvantages…
Cost is one of them. Four in-wheel motors will be more expensive to manufacture than one or two chassis-mounted motors.
Then there are practical problems. In-wheel motors have a tough life. They’re subjected to the same shocks and stresses as the wheel itself. Like the EV’s passengers, chassis-mounted motors are protected from lumps and bumps by the suspension, with extra isolation provided by mounting bushings.
In-wheel motors also present the problem of where to put the brakes, which are what’s normally found inside a wheel. Though regenerative braking can do much of the work of slowing down an EV, for safety reasons they also need to be equipped with friction brakes.
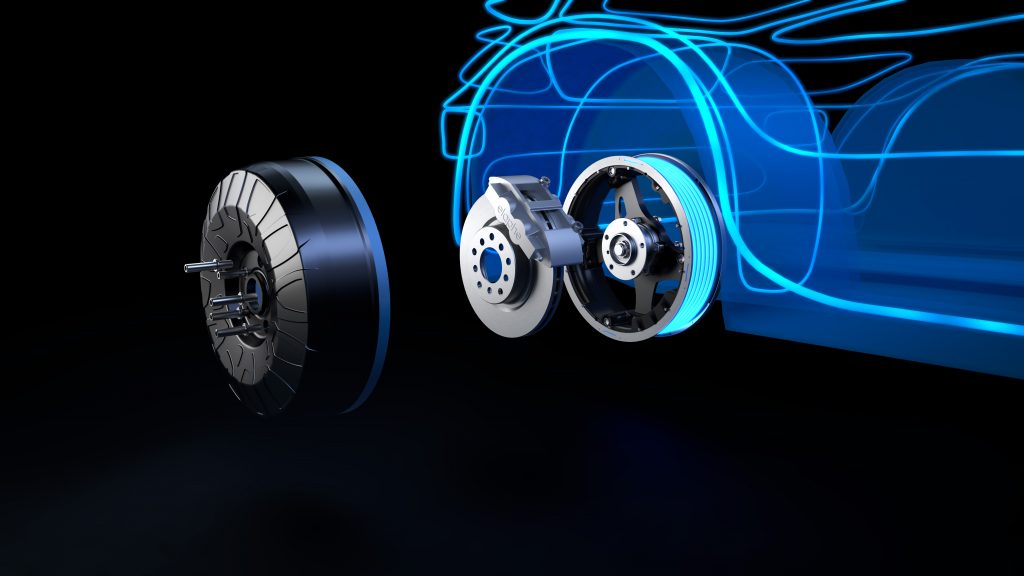
Another issue is that in-wheel motors add to what engineers call unsprung weight. Basically, they add to the weight that has to be controlled by the suspension system’s shock absorbers. So it’s more challenging for engineers to make an EV with in-wheel motors ride smoothly and handle well.
And in-wheel motors tend to be heavy things. This gets a bit complicated, so pay attention…
The torque output of an electric motor is proportional to the volume of its rotor. It’s not a problem to deliver strong torque, but power is another matter. Put simply, power is torque multiplied by motor revs and in-wheel motors don’t spin very fast. At 100km/h a typical-size wheel is turning at less than 1000rpm.
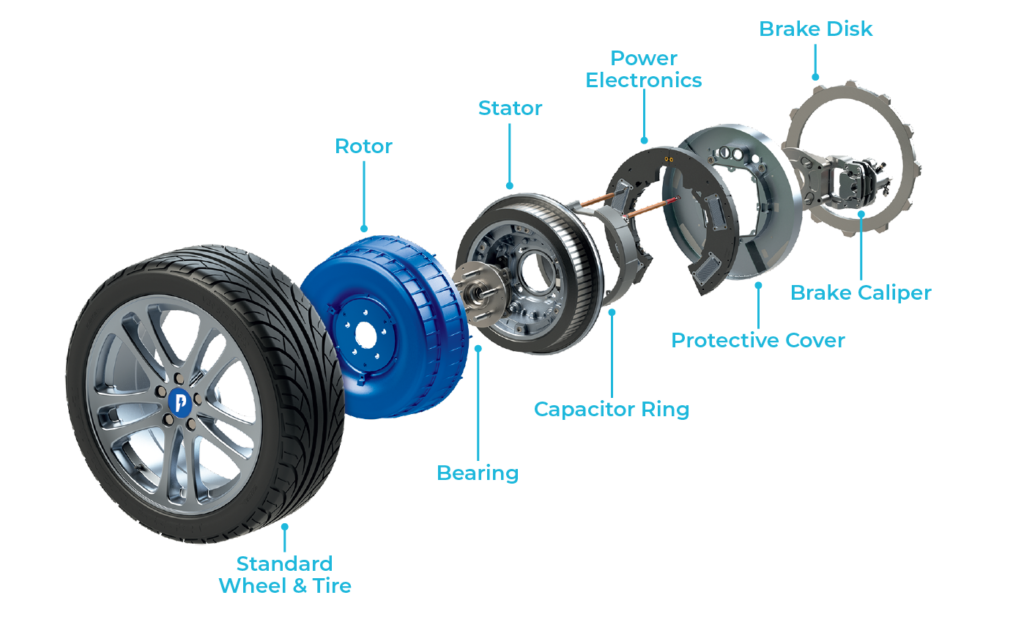
This inescapable relationship means in-wheel motors need big rotors to make enough power to deliver customer-satisfying performance. Since rotors are made mainly from magnetic steel, they’re heavy.
There is an alternative, and it’s the one currently preferred by all mainstream EV manufacturers…
They choose smaller motors that can easily spin to more than 10,000rpm. A single-speed gearbox that’s little more than two cogs in a case is used to multiply its lower torque output. With a differential, the motor can power two wheels. Even with these added components, a chassis-mounted electric motor assembly is a remarkably compact thing.
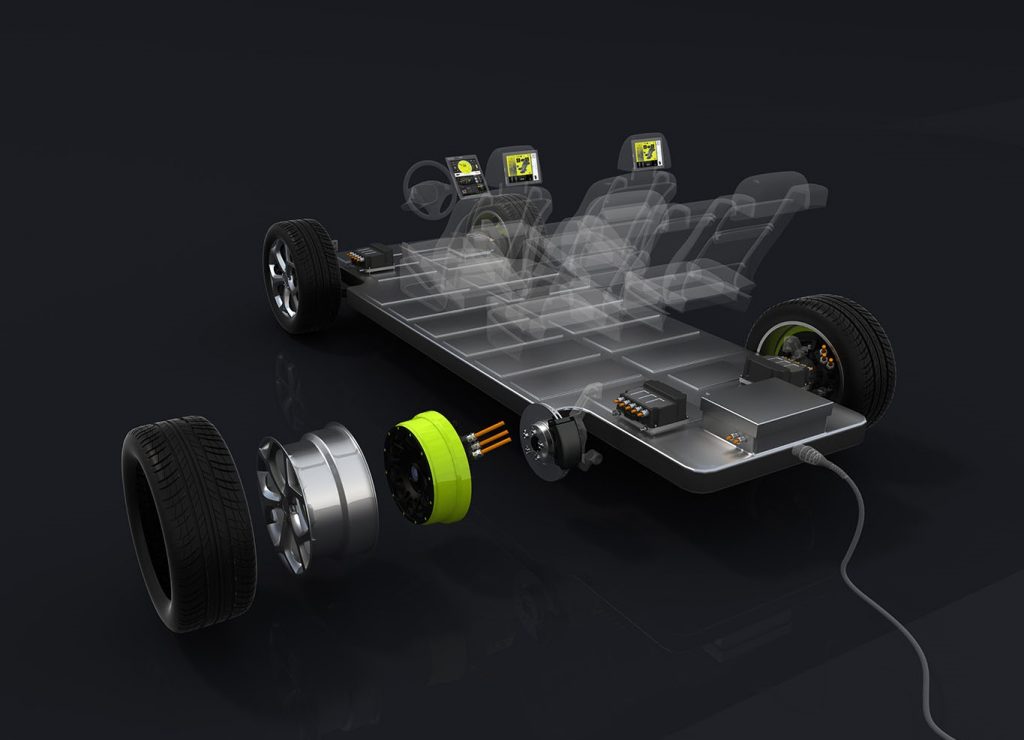
So, while in-wheel motors may save some space, their advantage isn’t as clear-cut as it might first appear. Then the issues of cost, shock-proofing, brake packaging and unsprung weight also have to be taken into account.
Add it all up, and it’s not hard to understand why EVs don’t have in-wheel motors. Maybe Lordstown, Lightyear and others will change the situation, but it seems unlikely they’ll change the minds of manufacturers using chassis-mounted motors with reduction gears and differentials.
An excellent analysis of in-wheel motor pros and cons, John. You also make a good point about the lack of EVs suitable for narrow parking places. Manufacturers seem to have decided that the solution to packaging occupants and their luggage while providing a range of 450km+ is to adopt increasingly wide skateboards. All fine in the US but European garages and villages were never designed for these vehicles.
Thoughtful article John. Perhaps the better compromise between one or two chassis mounted motors driving differentials is to use four chassis mounted higher RPM motors with (as you say) 2-cog gears driving each wheel (via CV joints to allow for both steering (at front obviously) and wheel suspension bounce (all four).
I note from eg RIversimple that use of super capacitors might greatly enhance regenerative braking as they are nearly instant at accepting incoming charge compared to chemical batteries. (And great at supplying near-instant extra power when needed)
I think Lotus did some research on the unsprung weight issue and concluded it was a matter for good suspension design and not a no-no, but certainly the environment to which an in-wheel is subjected is not great.
So perhaps the next article should be “Why don’t EVs have four near-wheel motors?” with “Yeh, why not!” added! There should be heaps of bonnet space after chucking out the ICE and all its 20th century stuff, but OK perhaps the boot/trunk space might suffer a bit.
We’ll get there!
Regards