Think all EVs are equally green? Think again
Produced in partnership with BMW
If you really want to make a greener motoring choice, you need to look beyond vegan interiors and renewable charging. Here’s how to know you’re making the most eco-friendly choice possible.
It’s obvious, really — driving an electric vehicle can only be truly, deeply green if the energy powering it is exactly the same colour. Using renewable, zero-emission energy to recharge is essential if the environmental benefit of an EV is to be realised.
An EV’s lifetime energy consumption pattern actually isn’t so different from other cars. Using it — otherwise known as driving around — is the phase that uses by far the most power. But we understand this, which is why most eco-conscious EV owners naturally choose to charge with green energy.
But there is another choice that is hugely important for the EV buyer to get right if they’re determined to maximise eco-impact. The second-biggest of the factors in a vehicle’s lifetime energy consumption is the manufacturing phase.
This is an even bigger deal for an electric vehicle than a car powered by an internal combustion engine (ICE). Why? Because it simply takes more energy to build an EV, which makes how they’re built a very big deal indeed.
The reasons are pretty straight forward. Compared with an ICE-powered equivalent, an EV is heavier. By hundreds of kilograms, typically. It simply takes more stuff to make an EV, and making that stuff consumes energy.
Most of the extra weight of an EV will be its battery pack, and these are especially energy-intense to make. To at least partially offset the extra weight of the battery, smart car makers often will choose to use lightweight material like aluminium and carbon-fibre where appropriate. Both are more energy-intense to make than steel.
So one of the most important moves for a car maker determined to reduce the environmental impact of producing EVs is to use green energy.
BMW is an undeniable leader in this field, with the German premium brand working towards greener manufacturing for years. Before commencing production of the innovative i3, back in 2013, the company made sure an array of wind turbines was installed beside its Leipzig factory to supply all of the electricity to run the car’s assembly line.

Today 100 percent of the electricity used by BMW Group production facilities worldwide is green. And that’s not just EVs, but for all its vehicles. The brand also focuses on sourcing power from regional providers close to its factories.
One of its newest plants, San Luis Potosi in Mexico, is powered largely by nearby photovoltaic solar panels. In Germany, the Munich and Dingolfing production lines for the new iX and i4 EVs comes from hydroelectric plants.
Between 2006 and 2019 BMW reduced its production emissions, taking all energy sources into account, not just electricity, by 70 percent. And it isn’t stopping there.
“We are pursuing clear targets to produce the greenest electric vehicle fleet by reducing the lifecycle CO2 emissions per vehicle by at least a third,” says Oliver Zipse, BMW Group CEO. “These targets centre on reducing the carbon footprint per vehicle by at least a third by 2030 compared with 2019 levels. The strategy includes reducing CO2 emissions by at least 80 per cent in the production phase, 40 per cent in the use phase and at least 20 per cent in the supply chain.”
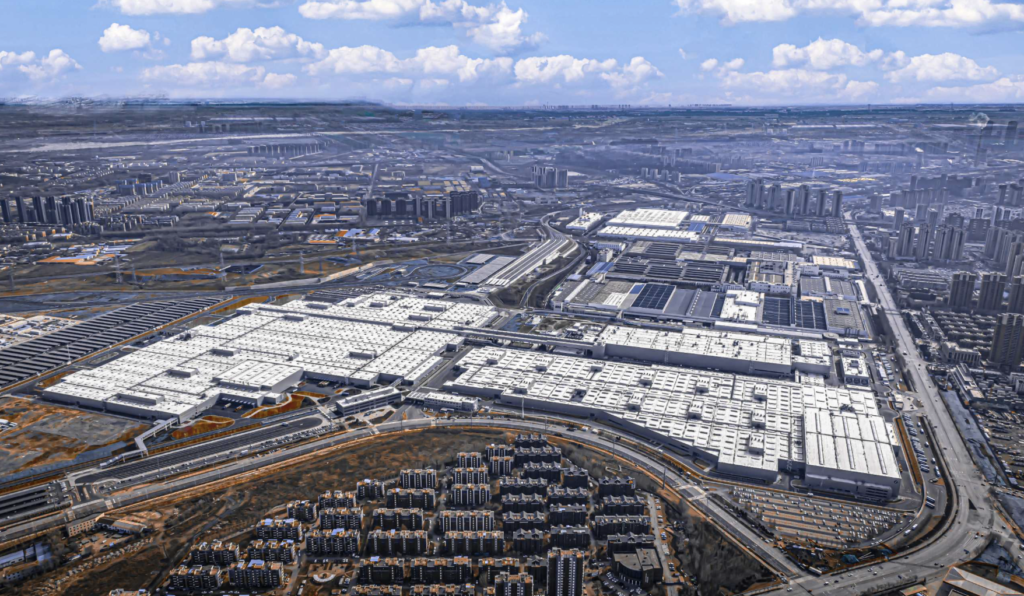
But the company also recognises that greening its own factories alone isn’t enough. Even larger amounts of energy are needed to power the processes to produce the materials and components from which a car is made.
BMW has been at the forefront of what’s known in the business world as supply-chain decarbonisation. Again the i3 provides an example of the company’s long-term commitment.
One of the most innovative features of the i3 was its carbon-fibre body. This lightweight material is more commonly found in hugely expensive sports cars. Producing it is incredibly energy intense, but BMW found a supplier in Washington State, USA, using only hydroelectricity to create the precious fibres.
Now BMW is making a similar move with steel. This is a hugely important step, as steel is what the bodies of the majority of the company’s line-up are mostly made from.
Steel production is a significant source of global CO2 emissions, chiefly because so much coal is burned to make it. But BMW has signed an agreement with a Swedish start-up which has developed a steel-production process that instead uses hydrogen and renewable electricity.
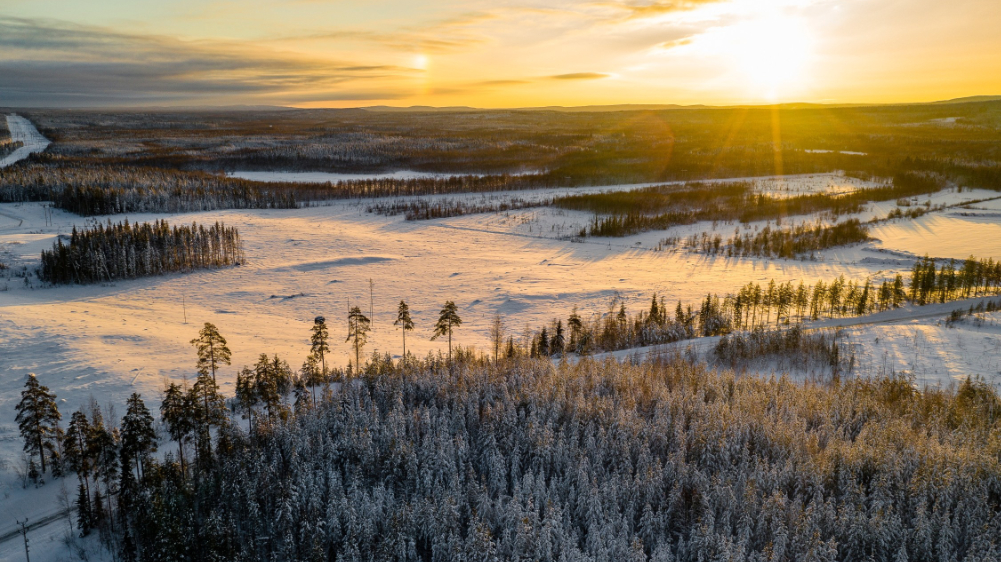
The steel-making method developed by H2 Green Steel cuts CO2 emissions by 95 percent. BMW aims to begin stamping bodies from the Swedish company’s product from 2025. The stamping scraps will be recycled, naturally.
And this deal, too, is just the beginning. “Our goal is to reduce CO2 emissions in our steel supply chain by about two million tonnes by 2030,” adds Zipse. “Sourcing steel produced using hydrogen and green power can make a vital contribution to this.”
The company is also moving to drastically cut the emissions associated with EV battery pack production. Two years ago BMW signed a long-term supply contract worth €2 billion for battery cells with the Swedish company Northvolt. The cells will be produced in Europe at Northvolt’s gigafactory from 2024.
BMW also sources EV battery cells from Chinese-owned CATL and Korean company Samsung SDI. For all EVs using the company’s fifth-generation electric drive technology – everything form the impressive iX3 and onwards – BMW is requiring all its suppliers to use only green power in their battery cell manufacturing.
The other fifth-generation change worthy of mention is a new electric motor design that doesn’t require magnets made from rare-earth elements. These are used by most other EV manufacturers, but the extraction and refinement of rare earths is a dirty business that’s best avoided.
Environmental impact isn’t the only criterion BMW looks at when choosing suppliers. It also considers societal issues. Working with its suppliers, the company has made big cuts to the amount of cobalt needed for its battery cells, and will source the vital metal only from ethical producers.
BMW takes similar care sourcing lithium, another vital ingredient of battery cells, for its suppliers. Since 2019 it’s had a lithium supply deal with an Australian mining company. Skyrocketing demand for EVs means BMW needs more lithium, so last year it added a second, US-based supplier.
This year BMW aims to sell more than 200,000 EVs worldwide, at least double the number it sold in 2021. A portion of this massive increase will come from the launch of two new EVs, the big i7 limousine and the small iX1 crossover SUV.
BMW’s approach to the particular challenges of reducing the environmental impact of manufacturing its growing line-up of EVs is truly comprehensive and unique. The measures discussed here are only the highlights. It would be easy to keep going, burrowing into the fine-grained detail of its programs for used EV battery packs to have a second life as stationary energy storage devices before eventual recycling.
Anyone with EV eco-questions will find that BMW has persuasive answers to all of them. This car maker understands that environmentally responsible manufacturing goes much, much deeper than a thin layer of recycled material in a few look-at-me locations… it goes all the way to the hidden but vital core of the car.