3D printing to make future Porsche EVs lighter, more advanced
Upcoming Porsche electric cars – including future iterations of the Taycan – could benefit from components manufactured using advanced 3D printing.
The promise of reduced weight, stronger components and smarter, more intricate shapes that may not have been possible using traditional manufacturing techniques has Porsche investigating ways to incorporate the advanced new manufacturing technique to make its future EVs faster and more agile.
The German sports car specialists worked with component supplier Mahle to develop pistons for its fastest supercar, the 911 GT2 RS.
Rather than mimic the design of the existing piston, engineers took the opportunity to redesign them.
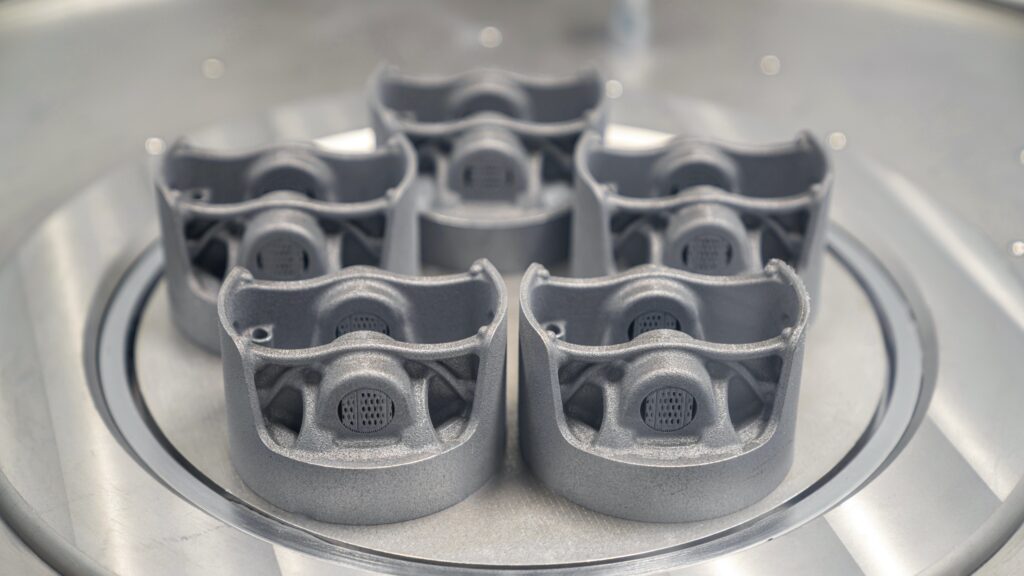
That allowed a 10 percent weight saving and an “integrated and closed cooling duct” to be added to the crown of the piston, which Porsche says would not be possible using the traditional forging manufacturing method.
“Thanks to the new, lighter pistons, we can increase the engine speed, lower the temperature load on the pistons and optimise combustion,” says Frank Ickinger from the advance drive development department at Porsche.
3D printing: layer by layer
Referring to it as “additive manufacturing”, the 3D printing process uses an aluminium alloy powder.
That powder is then heated and melted by a laser in fine layers using laser metal fusion (LMF).
The pistons that were created using the 3D printing process later successfully put through regular high speed validation tests required 1200 layers and took about 12 hours to produce.
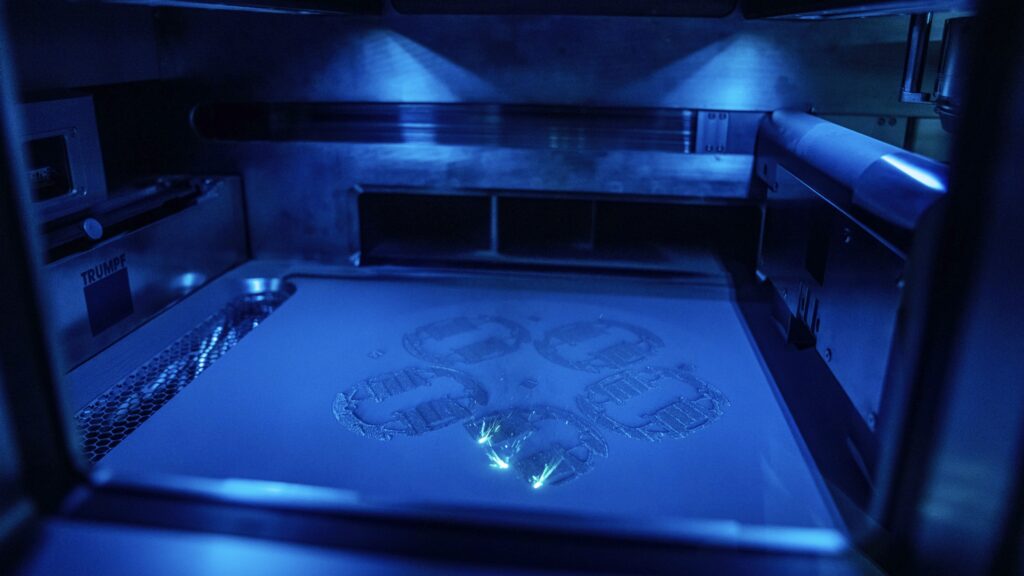
It’s a long manufacturing process, but one Porsche has been working on – and refining – for years.
Since at least 2018 Porsche has been considering 3D printing for EV components, with less weight and more complex shapes the goal.
And the new manufacturing technique appears to be getting closer for future Porsche electric cars.
“Using the example of a highly-integrated electric axle, we were able to also show the potential improvements not only in the product but also in its development process,” says Ickinger. “By applying new design methods, it has been possible to double the rigidity of the drive and reduce its weight by around ten percent.
“Thermal management was also significantly improved by the integration of a transmission heat exchanger while 12 components being built in allowed the omission of 30 screws, 12 seals and numerous other parts. This does not just create advantages in packaging, but also significantly reduces assembly work.”
Porsche also says copper can be used in the 3D printing process, something that “results in interesting concepts that offer great potential for electric motors”.
“The topic of cooling can also be taken to a new level for pulse-controlled inverters and motors,” Porsche also says.
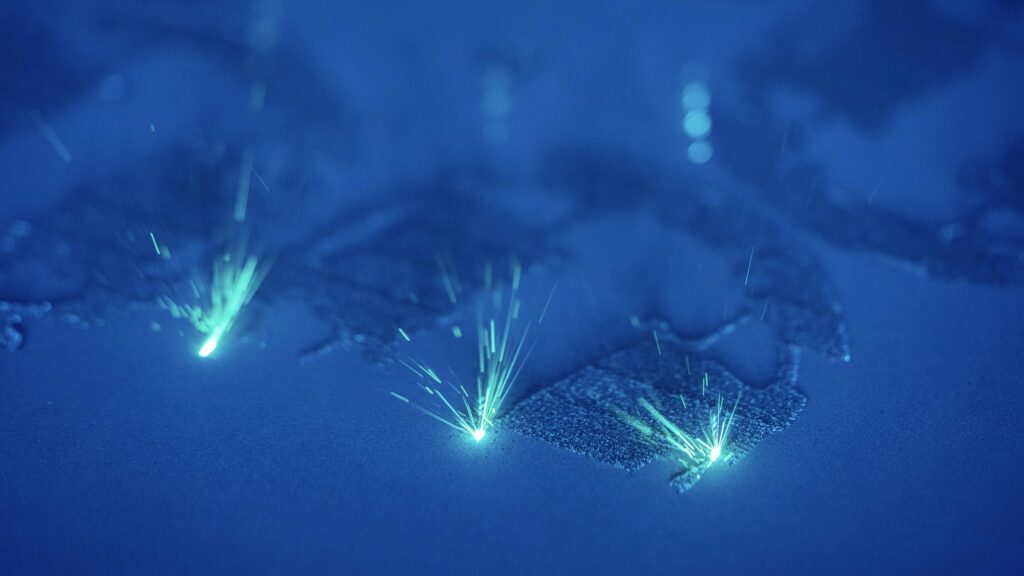
All with the aim of producing more power with less weight, which in turn has benefits for batteries; if engineers can lower the overall weight there’s theoretically a need for less electrical energy – or fewer batteries.
3D printing coming to Porsche soon
While 3D printing has been used in the automotive industry for decades for rapid prototyping – reducing the time required for testing prototype parts and building development vehicles – it has so far not been used on mass manufacturing.
That’s about to change.
“I am certain that additive manufacturing will be an established part of automotive development and production in 10 years’ time at the latest,” says Ickinger.
Between now and then there’s plenty of testing and validation to be done.
“From design to production and through to finish machining, there are a great many new parameters and influencing variables that do not exist with traditional methods of production. We are going to need to reliably master all of them in order to achieve uniform quality so there is still plenty of work to be done for a series production process in the automotive industry.”